Hydraulics have been around for thousands of years, likely originating in Egypt and Mesopotamia. By the 3rd century BC, positive displacement water pumps- known as Archimedes' Screw, were used for raising water in applications such as removing water from the hold of large ships. In Europe's early modern period of the 17th century, French physicist and mathematician Blaise Pascal made significant advancements in hydrodynamics, developing what we know today as Pascal's Law, which he applied to the development of the first hydraulic press.
Hydraulics Today
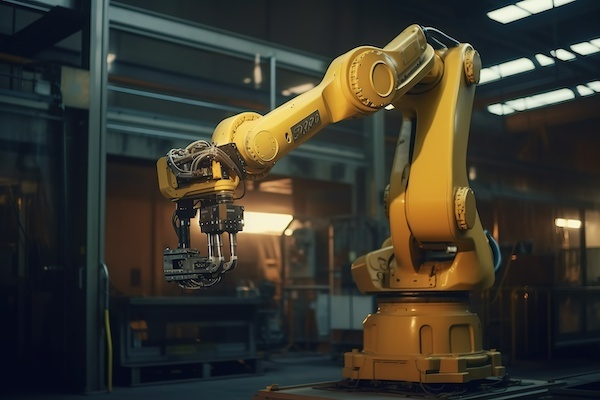
Today, hydraulic systems are used in virtually every industry including construction, agricultural and mining equipment, automotive, aerospace- and of course, manufacturing. Manufacturing facilities rely heavily on hydraulics for a wide variety of production activities to operate machine tools, robotics, conveyors, presses, material handling, die-casting, forging and much more. In these applications, hydraulics can provide tremendous power obtaining pressures of up to 690 bar (10,000 psi).
Leveraging the compression of fluids, hydraulics achieve significant amounts of power, transferred using less energy and providing greater efficiency than other methods such as pneumatics or electric motors.
The Future of Hydraulics in UK Manufacturing
At the 2022 Fluid Power & Systems exhibition held in Birmingham, the Fluid Power and Factories of the Future presentation was chaired by Paul Cooke, Interim CEO of the British Fluid Power Association (BFPA). Mr. Cooke discussed how with the advent of IoT the future factory will be flexible. All the production and assembly machinery will be smart, connected, configurable and fully automated. Moreover, in this factory of the future will be the next generation of production and maintenance managers and engineers. These people have been brought up in our digital world and are used to getting what they need using their smart devices.
Fluid power - continuing to drive industry
Against this digital backdrop, Cooke is convinced that fluid power will continue to play a critical role. "This is one of the key issues that I like to impress fluid power is important and will continue to drive industry," he said. "We will be as important tomorrow as we are today. Fluid power supplies the control and motion to ensure production in the UK keeps moving, and about 60 per cent of production in the UK in part depends on fluid power solutions and products."
Cooke stated the total market value of the fluid power industry in the UK and Ireland is approximately £1 billion. "So, today we remain very important and the way the industry adapts going forward is of course extremely important not just for the fluid power industry but also to UK's prosperity."
In today's Industry 4.0 factory, we have smart hydraulics to control systems and devices that deliver data in real-time to the plant floor. The data communicates to a collective network of connected devices which enables communication between devices, improving production efficiencies and cycle time while allowing for real-time equipment monitoring and enhancing preventive maintenance. All connectivity increases the effectiveness of fluid power.
Cooke went on to emphasize how modern control systems utilize open dialogue protocols. "From a smart device or desktop computer, you can change the production cycles of the machine <where> the future won't be like it was in the past <when> if you wanted to change the production cycle, change the parameters or introduce a new product to the manufacturing process you had to reprogram a PLC. This might take days and involve very expensive reprogramming. Today, we can change the system parameters from a tablet PC using open protocol."
Also speaking at the Fluid Power & Systems exhibition Martin Hoskins, Sales and Customer Development Manager at Bosch Rexroth, spoke about connected hydraulics within the future framework of the modern factory, When we think about connected hydraulics and the factory of the future, words such as permanent or fixed, or even phrases such as jobs for life, are old and not suitable for the new approach to business, he said. Mr. Hoskins discussed how we use words such as modularity, quietness, flexibility and efficiency. These are all words that benefit the environment and benefit industries, and this is where we've got to go. Through the years, we've worked very closely with various companies in production and have learned that IoT has a very forward-thinking benefit to designers, solutions providers and also the end-users and OEMs. By working together, we can develop the digitalization fight for the future.
Industry 4.0 Technology and Smart Hydraulics
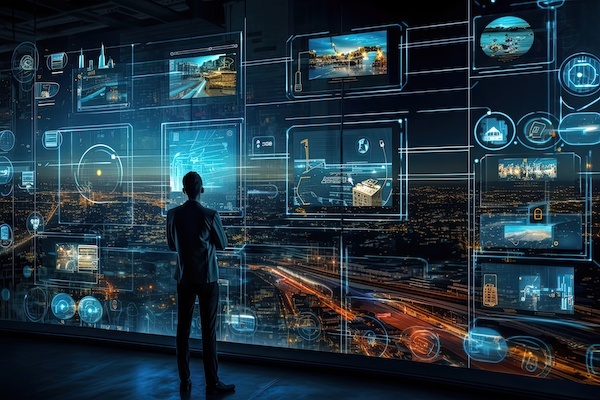
Smart hydraulics use the power of traditional hydraulics to integrate with the intelligence of electronics, increasing manufacturing efficiency. With sensors in components and equipment, process and operational data is collected to create a closed loop for automatically monitoring and operating systems.
Smart Hydraulics provide:
- Reduced energy consumption through smart systems that retrieve energy by lowering the pump's speed when the system is idle and running it only when necessary to maintain enough flow when not idle. This ability to adjust the energy consumption of the pump provides significant energy conservation.
- Predictive maintenance from variable frequency drives (VFDs) that are IoT enabled. A VFD is an electrical device that varies the input voltage of an electric motor to control its speed. VFDs control conveyors, fans, pumps and other industrial machinery. Instrumentation outputs go to the VFD allowing the system to acquire data that provides feedback for predictive maintenance to reduce costly downtime.
With IoT-enabled VFDs, each of these parameters are readily available to enhance data acquisition and management.
- Increased safety and longer service life because smart hydraulic pump systems run much smoother, reducing vibration and noise levels. Less noise increases worker safety, while decreased vibration allows for smoother operation, reducing wear on the system which increases service life.
- Maximum efficiency with smart systems that allow remote data transfer which expedites diagnostics and equipment control.
Conclusion
Industry 4.0 and the Industrial Internet of Things have bolstered Smart Hydraulics that are wirelessly controlled with remote monitoring, changing how engineers collect information, make decisions, boost efficiency and troubleshoot system problems in real-time. With enhanced monitoring of fluid control systems, engineers and their teams are tuned-in to machine functionality.
IIoT also provides the ability to be connected to the cloud, allowing any team member anywhere around the globe to receive real-time information and take necessary action from a single dashboard. Long-range Wide Area Networks (LoRaWAN) technology provides significant advantages for companies that use hydraulic systems as it can transmit operational data much further than local area networks (LAN). For instance, a General Electric engineer in Rugby can monitor and adjust a system at their factory in Dubai.
Industrial Automation and Process Research Analyst Kiravani Emani of Frost & Sullivan observed, "Electronic integration will continue to play a pivotal role in boosting demand for hydraulic products."
Sources include: